Officina
Since its establishment, the forge has been in Città della Pieve, in Umbria: a place with Etruscan-Roman roots and a supreme tradition in ironworking. Lispi beds are made of the highest quality iron, chosen with zero impurities, which is then wholly handcrafted, with fascinating processes and steps.
Since its establishment, the forge has been in Città della Pieve, in Umbria: a place with Etruscan-Roman roots and a supreme tradition in ironworking.
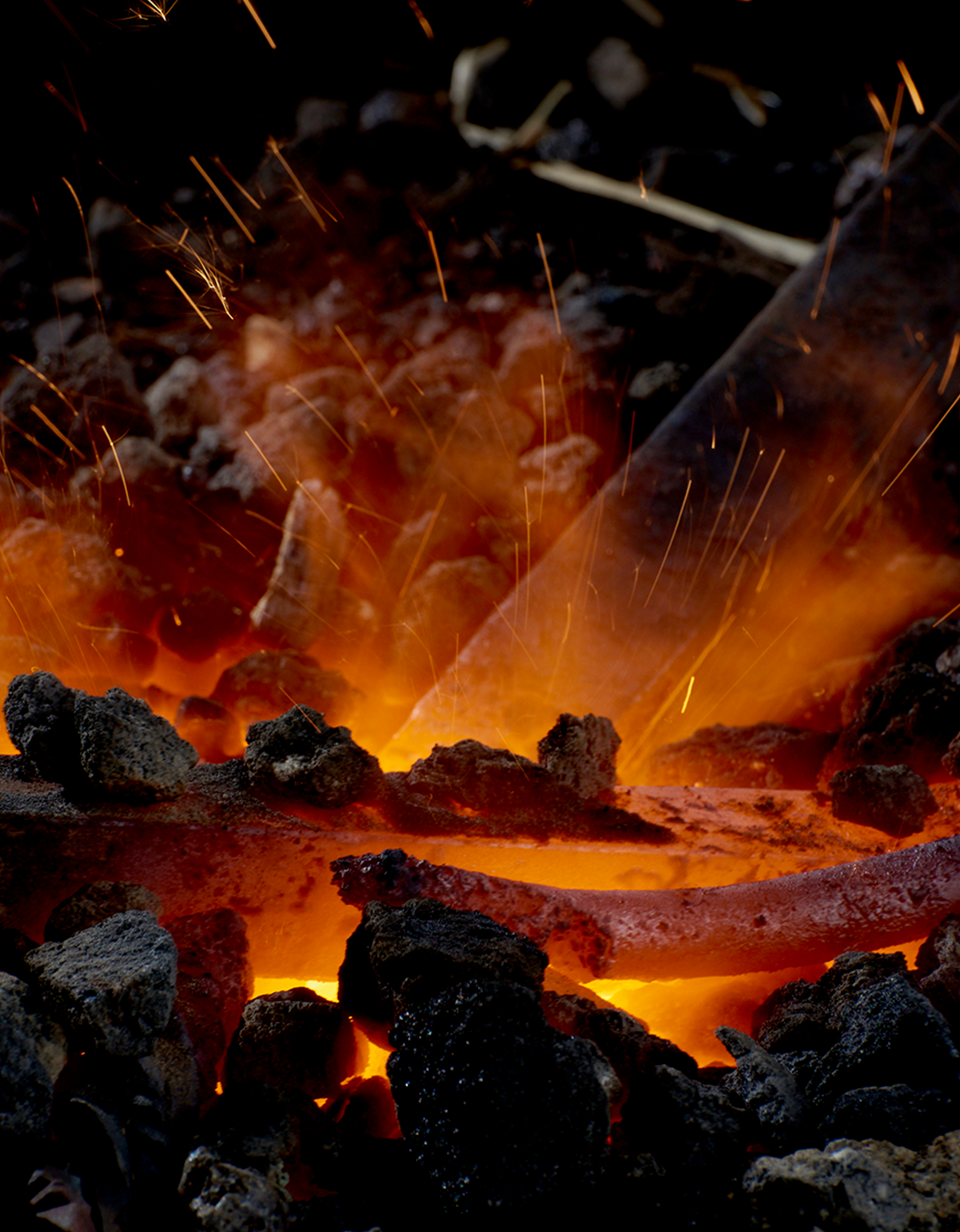
Iron is placed inside the burning hot forge. Once the iron has reached the right working temperature, it takes on its characteristic reddish colour.
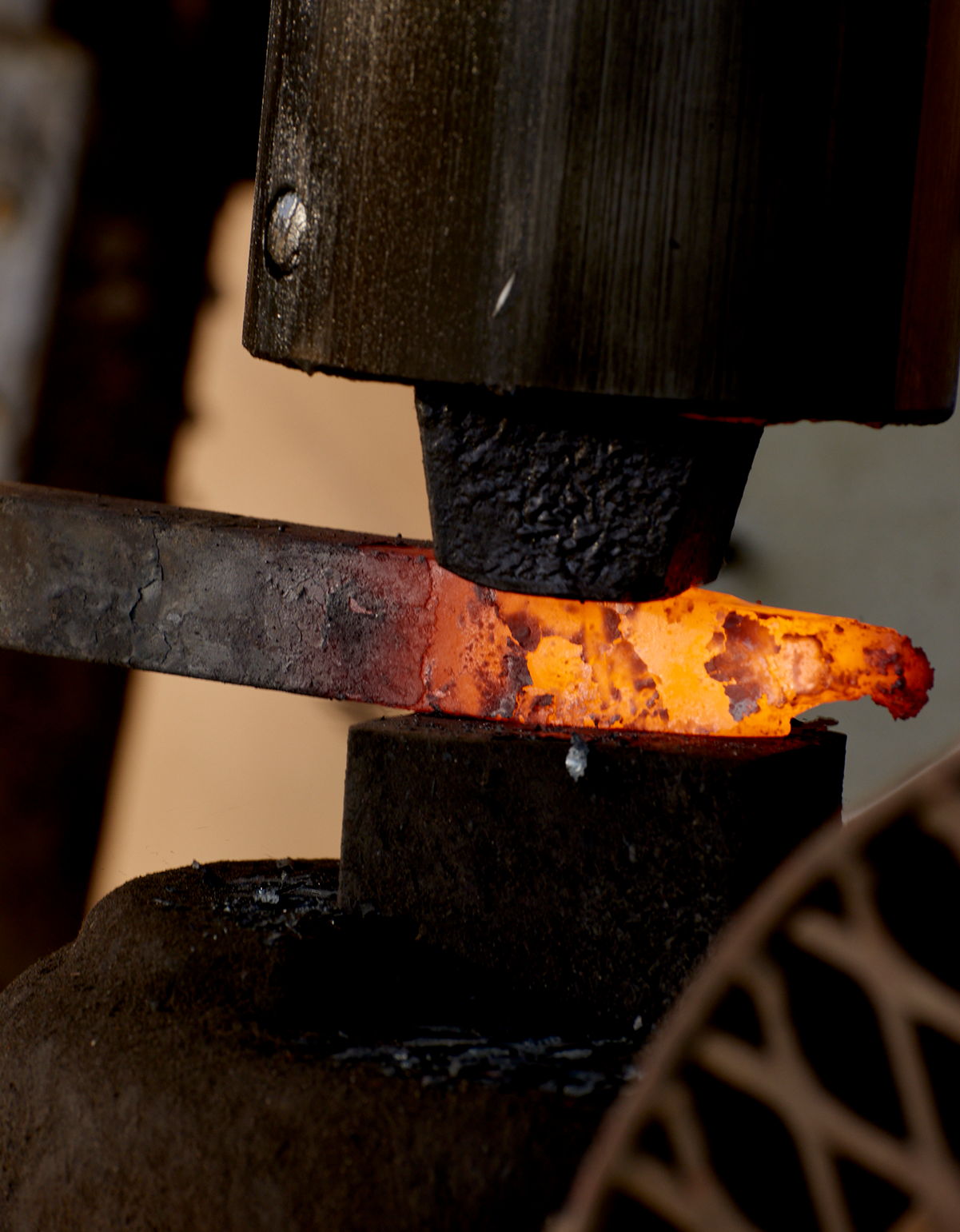
Iron in the forge, ready to be processed at working temperature (700-900 degrees).
Forged using a mechanical hammer.
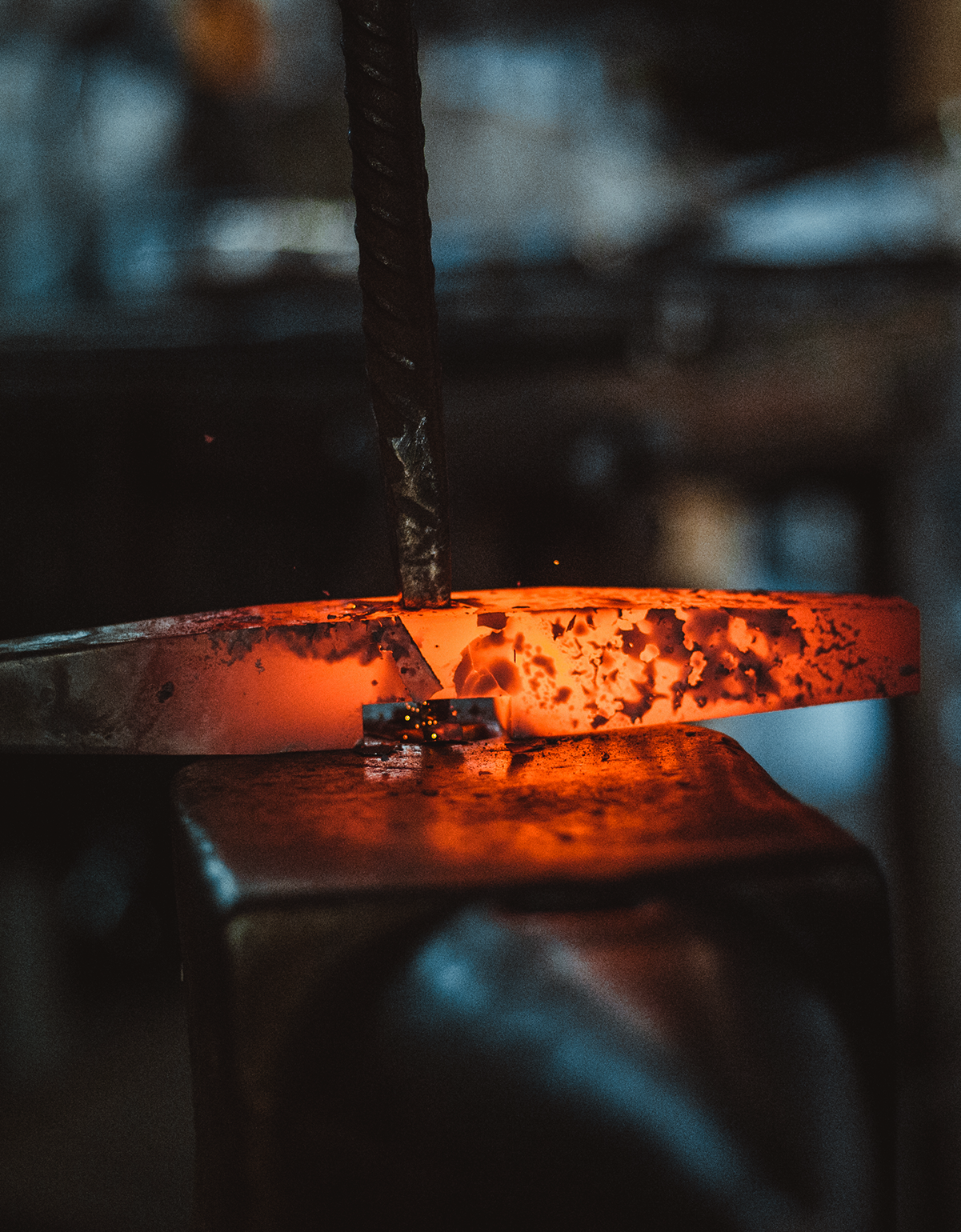
The ironworking process involves several stages, after cutting, depending on what needs to be done: beating, bending, welding, drilling, grinding, forging, assembling, painting in multiple stages, and firing.
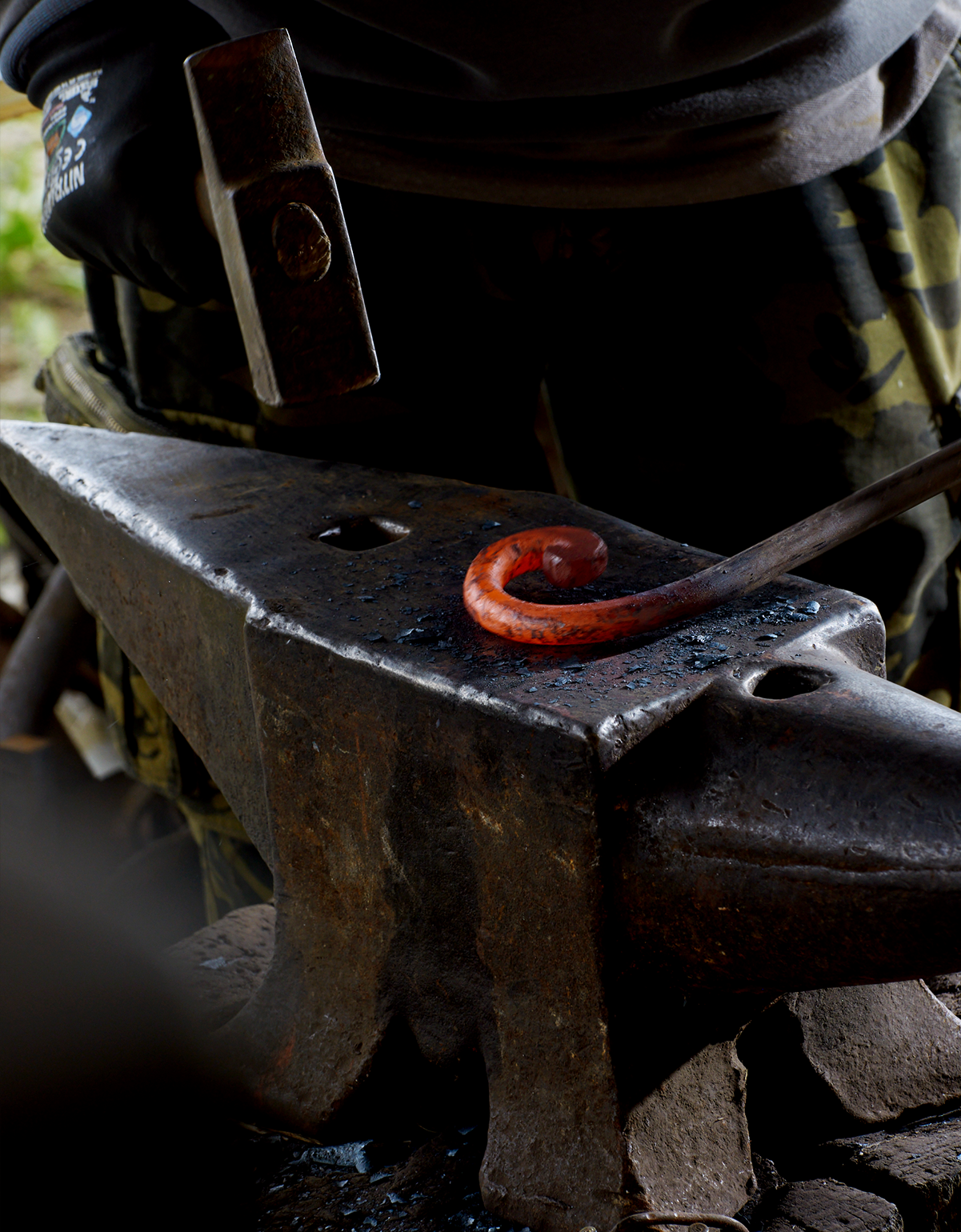
Forging the leg of a classic bed: a square hole is made with a punch.
The iron is beaten with a hammer on the anvil and shaped with several twists to modify its original structure and create different structures and decorations.
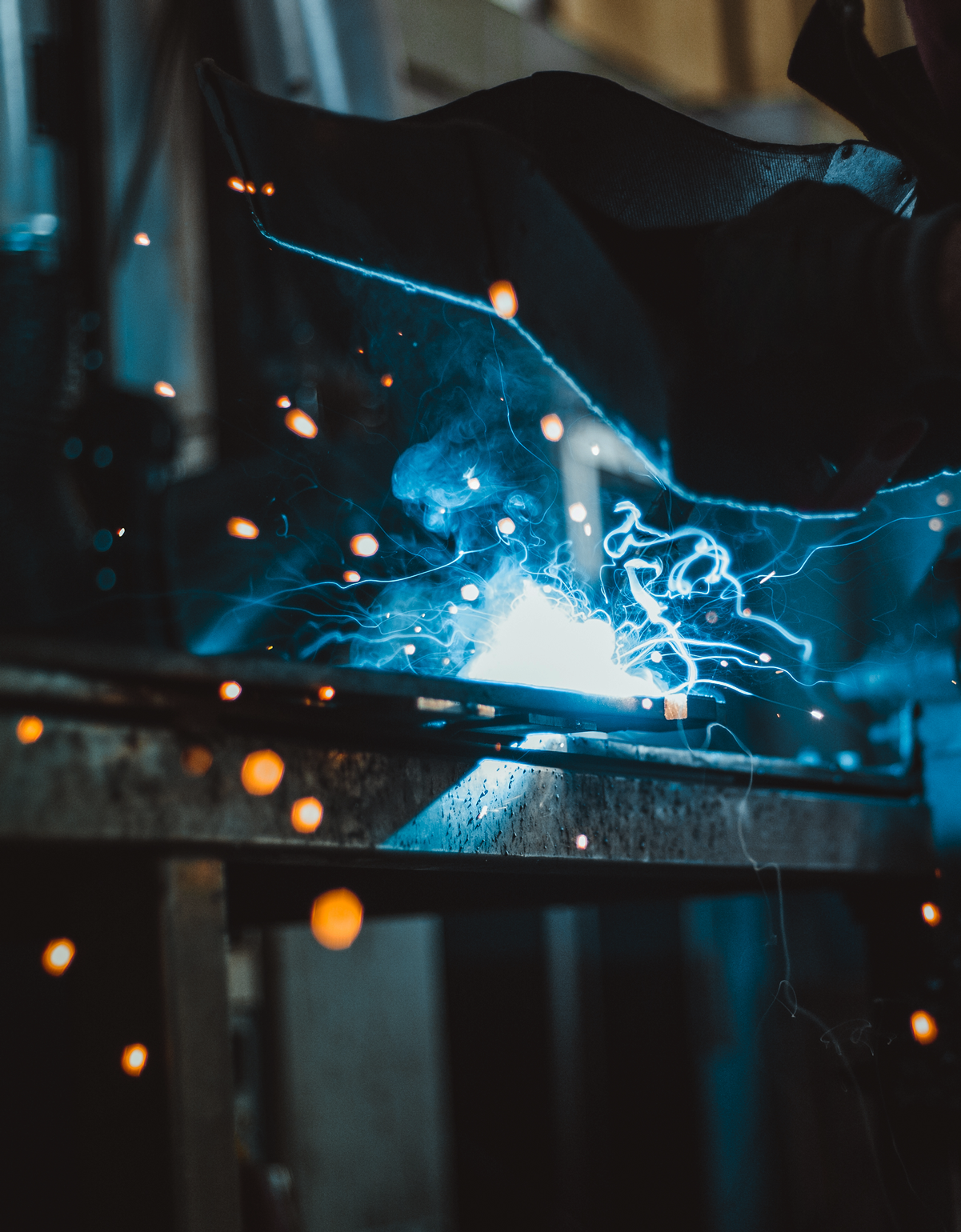
The creation of a four-poster bed is a lengthy process, punctuated by the rhythm of the blacksmith beating and shaping the iron on the anvil with great experience, technique, and care.
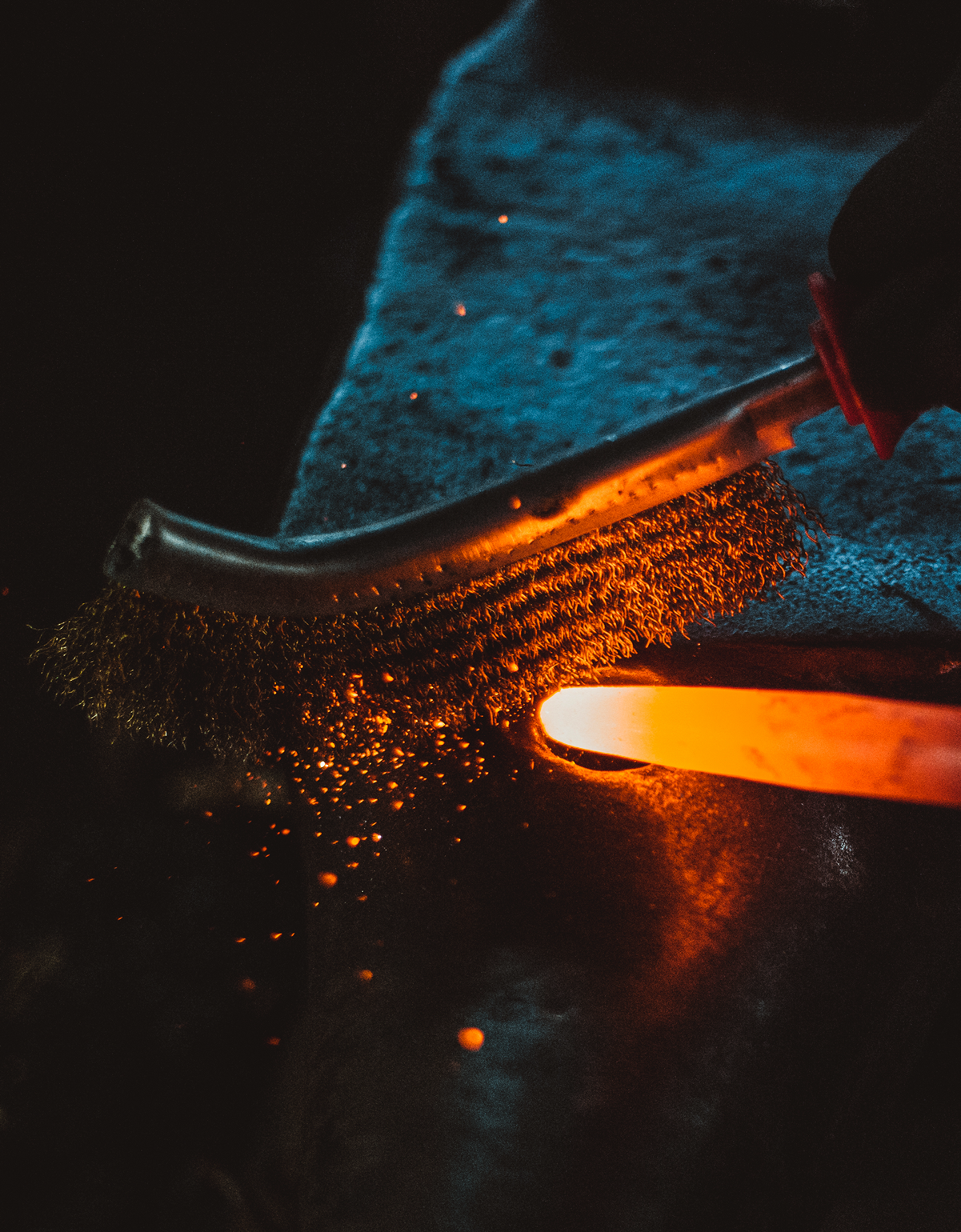
Metal electrode in inert gas (MIG) welding.
Brushing to remove impurities from the coal.